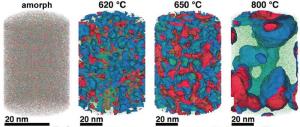
Korrosion frisst alleine in Deutschland jährlich 75 Milliarden Euro der Wirtschaftsleistung.
Welche Stähle und sonstige Legierungen davon betroffen sind und wie der Schaden begrenzt werden kann, lässt sich künftig möglicherweise besser abschätzen.
Denn ein internationales Team um Wissenschaftler des Max-Planck-Instituts für Eisenforschung in Düsseldorf hat einen amorphen Stahl aus Eisen, Chrom, Molybdän, Bor sowie Kohlenstoff analysiert und festgestellt, dass das Material desto leichter vom Rost angegriffen wird, je geordneter seine Struktur und je ungleichmäßiger die Verteilung seiner Atome ist.
Wenn die Elemente der Legierung kein regelmäßiges Kristallgitter bilden und sich völlig gleichmäßig über das Material verteilen, entsteht unter korrodierenden Bedingungen eine passivierende Schicht auf seiner Oberfläche, die es vor dem Verrosten schützt. Entstehen dagegen geordnete Nanokristalle, die mal mehr Chrom und mal mehr Molybdän enthalten, frisst sich die Korrosion rasch in das Material, weil sich keine passivierende Schutzschicht bildet. Die Erkenntnisse geben Materialwissenschaftlern Anhaltspunkte, worauf sie bei der Komposition und der Herstellung von Werkstoffen achten sollten.
An feuchter Luft nagt die Chemie an jedem Metall, es sei denn es handelt sich um Gold oder ein anderes Edelmetalle. Mit den weniger edlen Vertretern der Stoffklasse verbandelt sich der Sauerstoff der Luft jedoch nur zu gern. Feuchtigkeit hilft ihm bei der Partnersuche, und zwar umso besser, je salziger sie ist. Manche Metalle wie Chrom oder Zink überziehen sich am Anfang eines korrosiven Übergriffs mit einer dichten Oxidschicht, die weitere Annäherungsversuche des Sauerstoffs unterbindet. Bildet sich eine solche passivierende Schicht nicht, löst sich das Metall auf und zurück bleibt ein poröses und brüchiges Oxid, das eine Karosserie oder einen Schiffsrumpf allmählich zerbröseln lässt. Auf diese Wiese vernichtet Korrosion in den Industrienationen jährlich bis zu vier Prozent der Wirtschaftsleistung.
"Unsere Erkenntnisse erklären, warum manche Materialien besonders anfällig für Korrosion sind, obwohl sie genauso zusammengesetzt sind wie korrosionsbeständige Stähle", sagt Frank Renner, der die Studie am Max-Planck-Institut für Eisenforschung leitete. Aussagen über die Korrosionsbeständigkeit sind für Legierungen, die heute als Werkstoffe im Automobil-, Schiffs oder Anlagenbau verwendet werden, bisher noch schwierig. Diese Materialien bestehen aus zahlreichen Komponenten. Wie beständig sie gegen Korrosion sind, hängt nicht nur von ihrer Zusammensetzung ab, sondern auch davon, wie das Material verarbeitet wurde und welcher Temperatur es beim Einsatz etwa in einer Kraftwerksturbine ausgesetzt ist.
Ein Modell für den Übergang vom amorphen zum kristallinen Stahl
Das Team um die Max-Planck-Forscher hat nun erstmals umfassend untersucht, wie die Mikro- beziehungsweise Nanostruktur einer Legierung, die Chemiker mit der Formel Fe50Cr15Mo14C15B6 beschreiben, deren Korrosionsbeständigkeit beeinflusst. Die Legierung gehört zu den amorphen Stählen, die etwa als abriebfeste Beschichtungen Verwendung finden. Darin liegen die Elemente in einer unregelmäßigen Struktur vor, sind aber völlig gleichmäßig im Material verteilt. "Für uns ist die Legierung vor allem als Modellsystem interessant, in dem wir den Übergang von der amorphen zur kristallinen Form studieren können", sagt Frank Renner. Da sie gängigen Chrom-Molybdän-Stählen ähnelt, sind die Ergebnisse der Forscher auch für Materialien aus der Praxis relevant. Allerdings enthält die Test-Legierung der Forscher deutlich mehr Kohlenstoff als gängige Stähle, und auch der hohe Boranteil ist für Stähle aus dem Hochofen eher unüblich. Nur diese Mixtur ermöglichte es dem Team jedoch, die amorphe Variante der Legierung zu erzeugen.
Die amorphe Form der Legierung markierte den Startpunkt einer Messreihe, die über mehrere Zwischenstufen bis zur geordneten kristallinen Form führte. Wie weit die Legierung kristallisiert, hängt dabei von der Temperatur ab, bei der die Forscher die Elemente miteinander verbacken: Bei 550 Grad Celsius bleibt das Material amorph, während sich bei 800 Grad die vollkommen kristalline Form bildet. Die Zwischenstufen erhielten die Wissenschaftler bei 620 bis 670 Grad Celsius.
Die Nanostrukturen ihrer Stahl-Varianten klärte das Team mithilfe der Atomsonden-Tomografie auf. Dabei werden die Atome einer Probe eines nach dem anderen verdampft und von einem Detektor aufgefangen. Aus der Zeit, die ein Atom bis zum Detektor braucht, lässt sich auf das Element schließen, aus dem Punkt, an dem es auftrifft, auf seine Position in der Probe. So erhielten die Forscher genaue Karten der Materialien. An ihnen konnten sie nachvollziehen, wie sich die Atome mit steigender Herstellungstemperatur umgruppieren. "Dabei entstehen Bereiche, in denen sich jeweils ein Metall anreichert", erklärt Jazmin Duarte, die diese Untersuchungen anstellte. Die Probe, die die Materialwissenschaftler bei 620 Grad Celsius erzeugten bleibt dabei noch weitgehend ungeordnet. "Doch auch in dieser Probe lassen sich bereits kristalline Strukturen erkennen", so Jazmin Duarte. "Die bei 800 Grad erzeugte Form ist dagegen völlig kristallin, wobei sich die jeweils mit einem Metall angereicherten Bereiche über bis zu 50 Nanometer ausdehnen können."
Chrom widersteht der Korrosion am längsten
Die genauen Informationen über die Nanostruktur der Stahlvarianten verglichen die Forscher nun mit elektrochemischen Messungen, wie leicht die verschiedenen Formen zum Opfer der Korrosion wurden. Zu diesem Zweck benetzten die Forscher die Probenoberflächen mit einer Salzlösung und setzten die Legierung unter eine elektrische Spannung. Je höhere Spannungen eine Probe im Labor aushält, ohne sich aufzulösen, desto mehr Widerstand stellt sie dem Rostangriff auch in der Praxis entgegen. "Dabei erwiesen sich die völlig und die weitgehend amorphe Form als fast so beständig wie reines Chrom", erklärt Julia Klemm, die die entsprechenden Experimente gemacht hat. Reinem Chrom kann die Korrosion unter normalen Bedingungen wenig anhaben, weil es durch eine dünne passivierende Oxidschicht versiegelt wird. Eine solche Schutzschicht bildet sich auch auf den amorphen Stählen. In den größtenteils kristallinen Formen der Legierung ist das aber offenbar nicht mehr möglich. Hier frisst der Rost schon bei relativ niedrigen Spannungen Löcher in die Probe.
Um mehr über das zerstörerische Werk der Korrosion zu erfahren, analysierte das Team zudem, welche Elemente bei welcher Spannung aus dem Material gelöst werden. Zu diesem Zweck bedienten sie sich einer Methode, die Karl Mayrhofer am Düsseldorfer Max-Planck-Institut entwickelt hat: Dabei platzierten sie eine Kunststoffzelle mit einer Öffnung auf ihrer Probe. In eine solche Zelle führen von zwei Seiten Schläuche, sodass die Forscher von der einen Seite eine Salzlösung auf ihre Probe strömen lassen können, die sich auf der anderen Seite wieder auffangen lässt. Die ausströmende Lösung verdampfen sie mit einem Plasmastrahl und bestimmen in einem Massenspektrometer die enthaltenen Ionen.
"Unseren Messungen zufolge entweichen bei niedrigen Spannungen vor allem Eisen und Molybdän aus der amorphen Probe", sagt Julia Klemm: Das Chrom bleibt demnach zurück und bildet eine undurchdringliche Schutzschicht auf dem gesamten Material. Mit steigender Spannung wird jedoch immer mehr Chrom gelöst, während der Anteil des gelösten Eisens und Molybdän gleich bleibt oder sogar abnimmt. Ähnlich verhält es sich auch in der Probe mit nur geringem kristallinen Anteil. In der vollkommen kristallinen Probe werden molybdänreiche Areale mit steigender Spannung dagegen zusehends schneller zersetzt, während chromreiche Gebiete über einen größeren Spannungsbereich stabil bleiben. Im kristallinen Material verschont der Rost also die chromreichen Areale, und ein schwammartiges Material bleibt übrig.
Die Korrosion schafft ein poröses Material für Filter oder Katalysatoren
"Dass sich aus unserer Modell-Legierung elektrochemisch poröse Strukturen der sehr harten Verbindung aus Eisen, Chrom und Kohlenstoff erzeugen lassen, haben wir eher zufällig entdeckt", sagt Frank Renner. "Wegen ihrer sehr großen Oberfläche könnten sie sich als Membranen für Filter oder Trägermaterialien für Katalysatoren eignen." Denn sowohl Filter als auch Katalysatoren erfüllen ihre Aufgabe desto besser, je größer ihre aktive Oberfläche ist.
Für Karosserien, Flugzeugrümpfe oder Turbinenschaufeln ist ein kristalliner Chrom-Molybdän-Stahl, den der Rost perforiert, dagegen unbrauchbar. Warum sich auf den kristallinen Formen der Legierung keine passivierende Schutzschicht bildet, können die Forscher auch erklären. Da der Korrosionsschutz vor allem auf dem Chrom und seiner Oxidschicht beruht, bleibt das gesamte Material nur geschützt, wenn überall genügend Chrom vorhanden ist. Sammelt es sich dagegen in relativ weit auseinanderliegenden Arealen, werden nur diese Gebiete geschützt.
Der Zusammenhang zwischen Chrom-Verteilung und Korrosionsschutz gibt den Materialwissenschaftlern auch einen Hinweis, warum amorphe Stähle bereits durch einem Chrom-Anteil von vier bis fünf Prozent korrosionsbeständig werden, während dafür in kristallinen Stählen 12 bis 13 Prozent nötig sind: Letztere müssen insgesamt mehr Chrom enthalten damit auch in den chromärmeren Kristalliten genug vorhanden ist, um die passivierende Schicht über dem gesamten Material zu bilden.
Eine eindeutige Anleitung, wie sich Stähle aus der industriellen Praxis widerstandsfähiger gegen Rost machen lassen, können die Düsseldorfer Forscher zwar noch nicht geben. "Unsere Studie zeigt aber, dass bereits die Entmischung im Nanometerbereich stark beeinflusst, wie korrosionsbeständig ein Material ist", sagt Frank Renner. Dass sich alle Komponenten möglichst gleichmäßig in einem Material verteilen sollten, damit der Rost es nicht zerfrisst, könnte also ein Anhaltspunkt für die praktische Materialwissenschaft sein.
Zusatzinformationen:
Maria Jazmin Duarte, Julia Klemm, Sebastian Klemm, Sergiy Borodin, Karl Mayrhofer, Martin Stratmann, Aldo Romero, Milad Madinehei, Daniel Crespo, Jorge Serrano, Stephan Gerstl, Pyuck-Pa Choi, Dierk Raabe, Frank Uwe Renner:
Element-Resolved Corrosion Analysis of Stainless-Type Glass-Forming Steels.
In: Science; Vol. 341 no. 6144 pp. 372-376; 26. Juli 2013, DOI 10.1126/science.1230081
Quelle: Max-Planck-Institut für Eisenforschung GmbH, Düsseldorf
Aktualisiert am 29.07.2013.
Permalink: https://www.internetchemie.info/news/2013/jul13/rostschutz-durch-unordnung.php
© 1996 - 2025 Internetchemie ChemLin